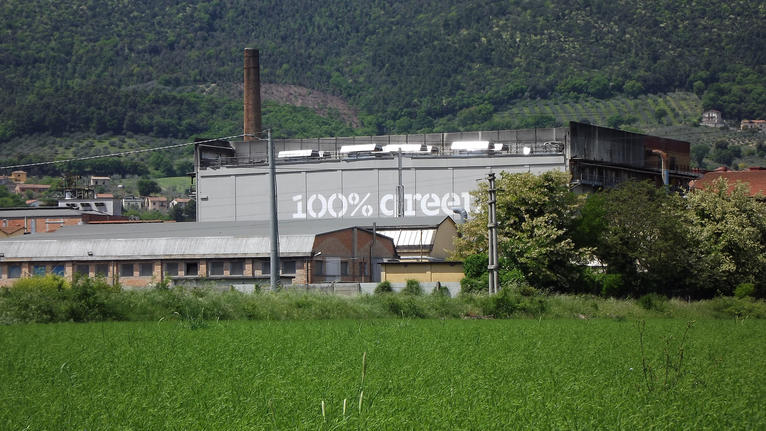
Acting to advance Sustainable Development Goals in our linoleum Green Factory
The United Nations adopted a set of 17 Sustainable Development Goals in 2015. Each of these goals provides guidance to businesses on how to contribute to a better future for the planet all the while being profitable. Here are some ways Tarkett is acting in its linoleum Green Factory in Narni (Italy) to advance Sustainable Development Goals.
Narni linoleum green factory is a mix of heritage and innovation
Tarkett’s Lino has been manufactured in the Narni factory in Italy since 1898. Historically, Narni’s strategic location overlooking a narrow gorge on the River Nera led the romans to fortify it as part of the ancient via Flaminia. In the late 19th century, the presence of a railway together with water from the Nera, fertile soil for growing flax, and the town’s position at the geographic centre of Italy made it ideal for manufacturing linoleum.
Built in 1889, the factory was subsequently acquired by Giovan Battista Pirelli and in 1898 became the Società Italiana del Linoleum. The Sommer Group acquired the plant in 1987 and merged with Tarkett in 1997. Tarkett has been improving the production processes and innovating ever since to make Narni become a Green Factory that continuously strives to make production processes even more environment-friendly. The efficiency of the production and the quality of the products have been continuously improved. Today the factory is accredited ISO 9001 (Quality System) and holds important environmental certifications including ISO 14067 (Greenhouses Gases – Carbon Footprint of Products), ISO 50001 (Energy Management System), ISO 14001 (Environmental Management System), OHSAS 18001 (Health and Safety Management System) and SA 8000 (Social Accountability).
Our teams at the Narni factory are taking sustainable initiatives in various fields.
Producing with Good Materials
The collaboration with local farmers has allowed for the cultivation of local linseed in fields neighbouring the Narni plant. One of the factory’s objectives for the near future is to collaborate with local farmers in order to extend the local linseed production and thus reduce our carbon footprint by using more local raw materials.
The local crops are performed in a responsible and sustainable way, without use of chemical fertilizers. The squeezing of the seeds and the consequent production of linseed oil, with the technical specifications suitable for our floor production, is made by local companies.
Producing and caring for People
The Mixing Line
- At Narni, the raw materials that staff manipulate during the production process are safe materials. They meet or exceed European regulations and standards and come from qualified and sustainable suppliers. For more information on European regulations regarding safe materials, please read article 33 of REACH Regulations (European Union Regulation EC1907/2006).
- There is a continuous increase in the usage of renewable and recycled materials. 94% of the materials are natural, 78% are renewable, 100% are recyclable. This aspect contributes to the well-being and health of people working on the mixing line.
Post Combustors to reduce VOC emissions
- Three post combustors have been installed to abate volatile emissions.
- More than 95% of the VOC (Volatile Organic Compound) emissions have been reduced, thus reducing the impact on staff’s health.
Using Resources Responsibly
Various types of equipment have been installed in the factory to reduce the consumption of natural resources and also have a positive impact on the production process.
- The factory has been equipped with three heat exchangers to recover the heat from post combustor oxidation, the post combustor trimming line and gas boiler emissions. This has enabled to reduce gas consumption by - 804782 m³/year.
- An Air Dryer equipment heats and dehumidifies the suppled air inside the ovens. This system is being expanded to more ovens and enables to:
- reduce the time needed to cure the linoleum flooring by 7 days,
- reduce oven gas consumption by -59136 m³/year
- reduce CO2 emissions by – 117 ton/year - During the calendering process, wastes, process scraps and end-of-use products enter into a biological or technical cycle. The closed cycle we implemented enables to recover linoleum paste as well as jute and powders during the process in order to reuse them to replace virgin raw materials. There is no production waste that goes to a landfill.
- A biomass boiler has been installed: it is fed with internal biomasses and when they are boiled, it produces hot water to heat the ovens. The biomass boiler enables to:
- Reduce oven gas consumption by - 278540 m³/year
- Reduce CO2 emission by - 552 ton/year - The eastern oven is thermally insulated to increase the plant energy efficiency. The insulation is being expanded to all of the other ovens. The insulation enables to:
- Reduce oven gas consumption by –106000 m³/year
- Reduce CO2 emission by - 215 ton/year
- Reduction of the curing time of linoleum by 2 days per oven - The Trigeneration System is the simultaneous production of electricity, heating and cooling power from a single device (gas engine). By cooling of fumes of the engine, it is possible to obtain high temperature heat to be used for the production of superheated water for the curing process in ovens dept. The heat recovered from cooling circuit of engine is used to generate hot water. This fluid feeds an absorption refrigeration unit to produce cold water at 17°C. This enables to have: - Higher efficiency of thermal and electricity production - Reduction of CO2 emissions (- 184 tons/year)
- The Recycling Department recovers post production and post installation scraps. Thanks to this action, the disposed scraps have been reduced by 70% vs 2007 and 1.600.000 kg of linoleum powder are reused in the process and thus replace virgin raw materials
- 3 closed water cycles have been set up in the oxidation department, the trimming line and the mixing line. Thanks to these closed cycles, 100% of the industrial water used in the production process is either recycled or recirculated.
- An evaporator recovers the condensation coming from compressors. The water closed cycle enables to recover the water from the evaporator to be used in the cleaning of the oxidator. In total, this equipment has reduced our water consumption by 80.000.000 liters/year.
- The roof of the building that houses the technical office and R&D laboratory is equipped with a photovoltaic system. The electrical consumption in the building has been reduced by 65000 kWh/year and CO2 emissions have been reduced by -29 tons/year.
- A low enthalpy geothermal system has been built in order to be integrated in the existing heating and cooling of the office building. This system has contributed to reducing CO2 emissions by -124 tons/year and to reduce gas consumption by – 61806 m³/year.
- Rain water recovery has been organized on the covered area (26,190 m²) of the plant. This has an immediate effect on the shortage of “fresh water” because less “drinking water” is used in the production process because it is replaced by rain water. Rain water recovery also avoids the overload of sewage networks in case of heavy rain.
This is what we are currently doing in our Green Factory to make linoleum floorings that are sustainable for people making them as well as people walking and living on them.
Our 2020 objectives?
- Double the volume of collected post-installation or post-consumer linoleum vs 2010
- Maintain 100% recycled/recirculated industrial water (closed-loop)
- 60% reduction of GHG (Greenhouse Gas) emissions vs 2010 - 28% reduction in energy consumption (KWh/m²) vs 2010
Interested in our initiatives at our Narni Linoleum Factory?